Efficient overall process chain for the production of integral, thermoplastic composite aircraft frames
Composite structures cannot yet compete with conventional metal structures in terms of manufacturing costs and cycle times. The aim of the project is to realize a cost-efficient process chain for composite aircraft frames with short cycle times.
The project OSFIT »One-Shot-Fully-Integrated-Thermoplastic-Frame« (FKZ: 20W1706D) comprises the development of an overall process chain suitable for series production for a composite aircraft frame with a thermoplastic matrix.
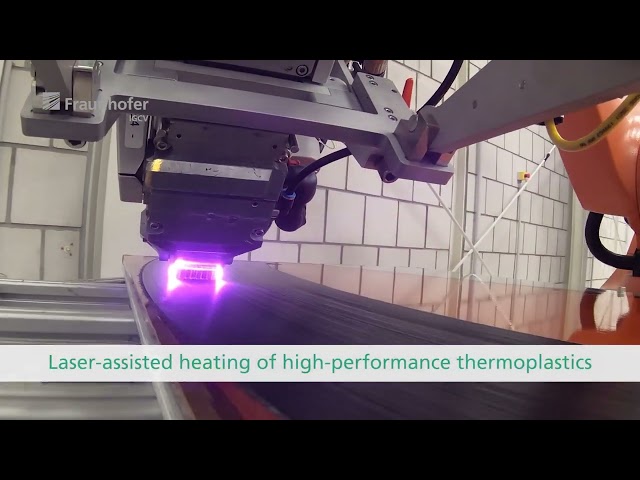
Privacy warning
With the click on the play button an external video from www.youtube.com is loaded and started. Your data is possible transferred and stored to third party. Do not start the video if you disagree. Find more about the youtube privacy statement under the following link: https://policies.google.com/privacyVideo OSFIT: One-Shot-Fully-Integrated-Thermoplastic-Frame