Fraunhofer IGCV welcomes new director Prof. Dr.-Ing. Rüdiger Daub
The Fraunhofer Institute for Foundry, Composite and Processing Technology IGCV (Augsburg, Germany) has a new director: On June 1, 2021, Prof. Dr.-Ing. Rüdiger Daub started as the third member of the steering committee. In this position, he will be heading the institute together with Prof. Dr.-Ing. Klaus Drechsler and Prof. Dr.-Ing. Wolfram Volk. Building on his extensive experience in the automotive industry, Rüdiger Daub will focus on production and processing technology as well as on e-mobility research. Among other things, he will drive forward the increasingly important topic of battery cell production. The appointment to the institute’s management also encompasses a call to the Technical University of Munich (TUM). There, Professor Daub will head the newly established Chair of Production Technology and Energy Storage Systems at the Institute for Machine Tools and Industrial Management iwb.
In his dual role as Fraunhofer IGCV director and TUM chair holder, Rüdiger Daub will further strengthen cooperation and synergies between these institutions. “I am excited to transfer research results into application-oriented projects – this is how impact is created,” says Daub. To this end, one primary research focus at Fraunhofer IGCV will be battery cell production: “At BMW, the manufacture of lithium-ion cells has fascinated me from the very beginning. However, the technical complexity of their production process is a challenge. At the same time, we as a society need these energy storage devices to be able to shape a sustainable future,” Daub emphasizes. “Personally, it was an exceptional experience to be part of establishing the BMW Battery Cell Competence Center – a platform to improve all the properties of battery cells continuously.” According to Daub, such concepts are necessary to develop and produce internationally competitive, sustainable products in the future. “Research in the field of battery cells strengthens and secures the competitiveness of Germany as an international technology hub.”
Ready for the research of the future
The institute’s directors Klaus Drechsler (executive) and Wolfram Volk consider the new colleague a perfect addition. “Fraunhofer IGCV is an important industry partner for research and development of production technology. In Rüdiger Daub, we have gained an accomplished expert in the field of technology development who, with his positive and inventive spirit, fits our institute and its visionary culture in every respect,” says Drechsler. Thus, management will continue its tried-and-tested model of the three-person team once again. Wolfram Volk adds: “We believe in a living culture of cooperation across teams and departments – among employees as well as in management. In this sense, we are particularly pleased that Mr. Daub has accepted the call from industry back to science. Welcome to Fraunhofer IGCV!”
More information
About Professor Dr.-Ing. Rüdiger Daub
Before his appointment to Fraunhofer IGCV and Technical University of Munich (TUM), Rüdiger Daub spent almost nine years in technology development at the BMW Group. Daub studied electrical engineering and information technology at the Karlsruhe Institute of Technology (KIT) and then worked as a research associate at the TUM Institute for Machine Tools and Industrial Management iwb. There he earned his doctorate in the field of laser materials processing. After completing his doctorate, he joined the BMW Group, where his last position was Head of Technology Development and Prototype Construction and where he was responsible for electrode production.In addition to prototype production, he helped establish the Battery Cell Competence Center, whose goal is to advance battery cell technology and optimize production processes. Since June 1, 2021, Daub has been one of three directors at Fraunhofer IGCV.
Fraunhofer IGCV – production engineering research that drives the industry forward
Fraunhofer IGCV stands for application-driven research with focus on efficient engineering, networked production and smart multi-material solutions. At the Augsburg and Garching sites, the almost 120 scientists in the three interdisciplinary scientific fields of casting, composite and processing technology conduct research into industry-ready solutions for more efficient production:
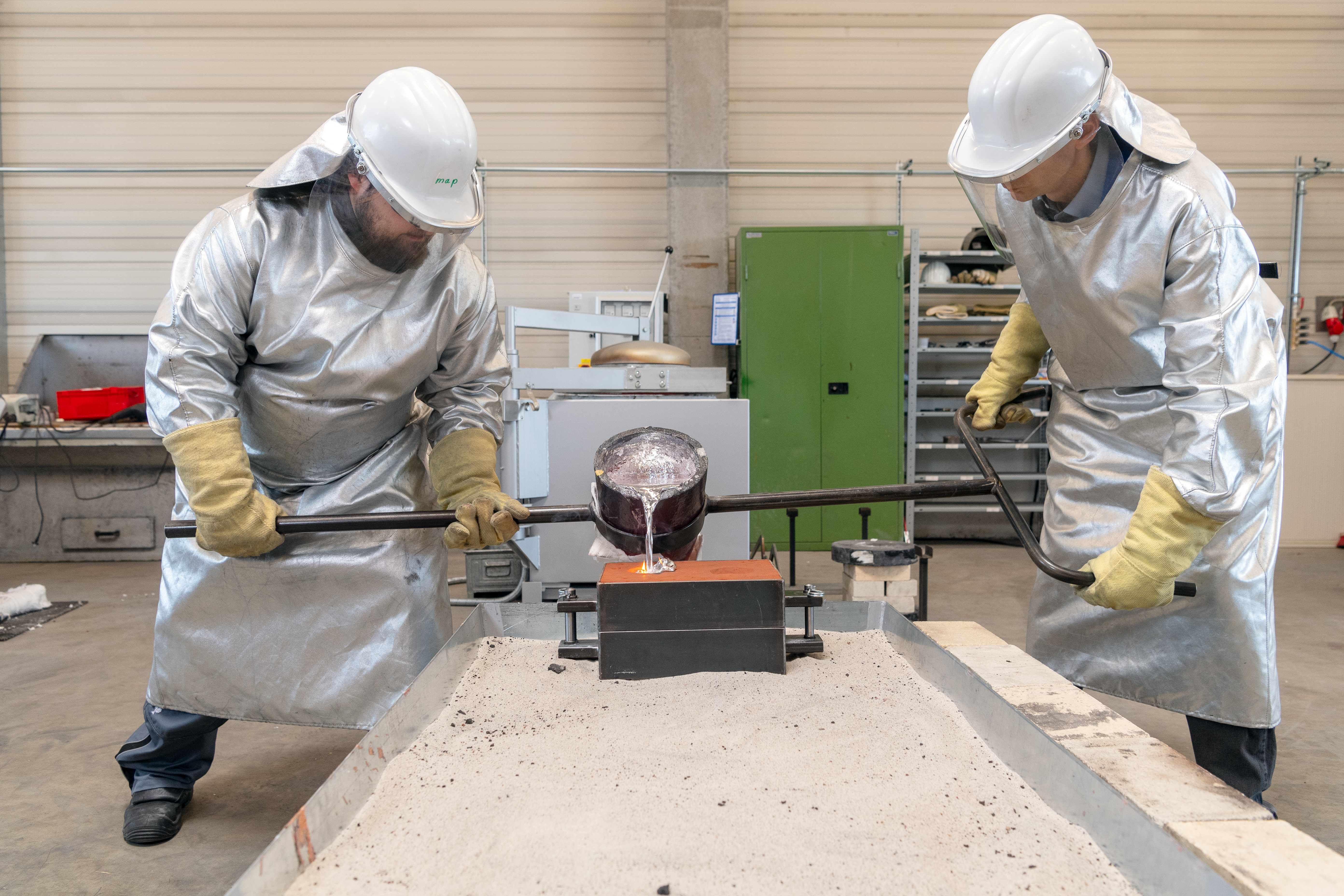
CASTING TECHNOLOGY – Head: Dr.-Ing. Steffen Klan
At the Fraunhofer IGCV Garching site, researchers focus on the future scenarios and topics of the casting industry. Core competences include indirect additive manufacturing, molding materials, casting materials, process development, analytics, and simulation. This combination represents an excellent starting position for interdisciplinary research. The researchers were able to show, for example, that topology-optimized components with the appropriate molding and casting process can contribute immensely to the process: CO2 emissions are reduced and – by creating a more flexible production – value chains become more resilient at the same time. Process stability and resource efficiency are also important areas of research. The researchers have already been able to demonstrate the potential that foundries show in various digitization projects.
COMPOSITES - Head: Lazarula Chatzigeorgiou
In the area of composites, the research focus is on automated, networked, and highly efficient CFRP manufacturing technologies. The researchers are also working on the digitalization of CFRP production processes and Industry 4.0 in the lightweight construction context; the Online Process Monitoring team implements this. Furthermore, the Materials and Testing Technology department develops smart materials, ensures the qualification of materials and focuses on hybrid construction methods. The researchers are also concerned with efficient recycling strategies. These include those already applied to the component planning process, as well as strategies to be implemented after the use phase of corresponding products. The main focus is on pyrolysis for the recovery of expensive carbon fibers and their further processing in a new, highly innovative wet nonwoven plant. Innovative CFRP manufacturing technologies are in exceptionally high demand in the aerospace industry: Alongside the transport and automotive industries, this sector – with the new field of urban mobility - is the primary user of the holistic CFRP expertise of Fraunhofer IGCV. There are many outstanding examples of application-oriented joint research work with industrial partners. At Fraunhofer IGCV, for instance, the CFRP sandwich shell components for a high-speed helicopter were manufactured automatically using Automated Fiber Placement (AFP). Similarly, the CFRP door frame for the Airbus A350-1000 is an outstanding example of the benefits of long-term cooperation, both in the context of funded projects and in bilateral, direct cooperation: the AFP-manufactured CFRP door has extensive advantages over its metallic counterpart and just recently entered series production. The results speak for themselves: With its intelligent lightweight construction strategies and its comprehensive, holistic know-how of processes and materials, Fraunhofer IGCV enables a clear technological lead. This means that small and medium-sized companies also benefit from the ecological and economic advantages in process and component development.
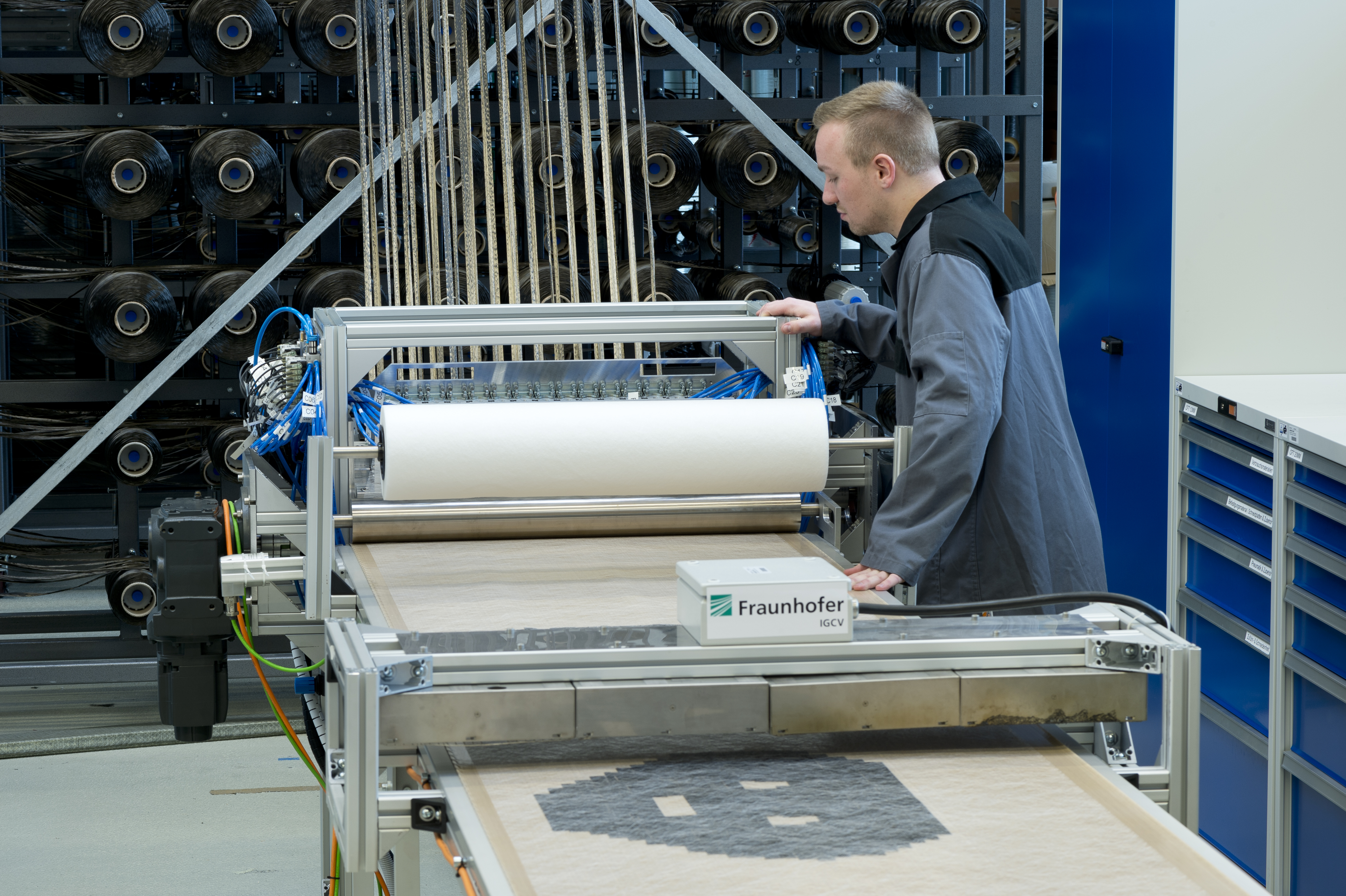

PROCESSING TECHNOLOGY - Head: Dr. Ing. Peter Barth and Prof. Dr.-Ing. Johannes Schilp (deputy)
Since November 2020, Dr. Peter Barth has been heading the Processing Technology division. He is pleased to have switched to a research institute after 19 years in the industry at technology leader Bosch: “My heart beats for materials, process technology and production! At a research institute, I can deep dive into technology again, and at the same time keep an eye on the big picture in my management function. It's also an opportunity for me to support SMEs in the region with applied research and develop solutions as well as competitive advantages with them.” Together with Prof. Dr.-Ing. Johannes Schilp, he shapes the strategic, scientific and operational orientation of Processing Technology. The departments' research activities range from a holistic view of a sustainable and energy-efficient factory (and production systems within it) to additive manufacturing processes as well as technical cleanliness and quality. This results in solutions focused on processes, components and assemblies as well as innovative automation solutions that incorporate the needs of employees in production. For example, the SynErgie project in the Augsburg model region is currently investigating the energy-flexible design and control of industrial production processes. This prepares the factories of the future to be integrated into the regenerative energy supply – and thus contributes to achieving climate targets.
About Technical University of Munich (TUM)
With more than 600 professors, 45,000 students and 11,000 employees, the Technical University of Munich (TUM) is one of the most research-intensive technical universities in Europe. Its focus is on engineering, natural sciences, life sciences and medicine, linked with economics and social sciences. TUM acts as an entrepreneurial university that promotes talent and creates added value for society. In doing so, it benefits from strong partners in science and business. It is represented worldwide by the TUM Asia campus in Singapore and liaison offices in Brussels, Mumbai, Beijing, San Francisco and São Paulo. Nobel laureates and inventors such as Rudolf Diesel, Carl von Linde and Rudolf Mößbauer have conducted research at TUM. In 2006, 2012 and 2019, it was named a university of excellence. In international rankings, it regularly ranks among the best universities in Germany.
Last modified: